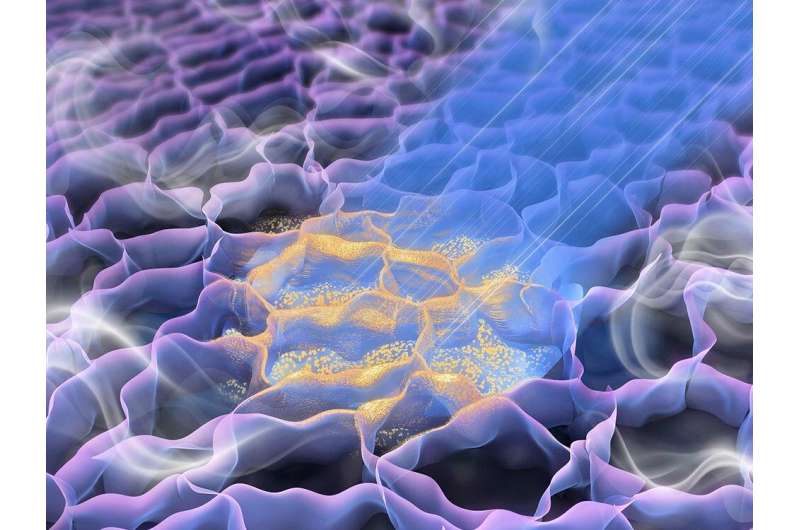
When used as wearable medical units, stretchy, versatile fuel sensors can determine well being circumstances or points by detecting oxygen or carbon dioxide ranges within the breath or sweat. Additionally they are helpful for monitoring air high quality in indoor or out of doors environments by detecting fuel, biomolecules and chemical compounds. However manufacturing the units, that are created utilizing nanomaterials, is usually a problem.
Penn State researchers lately enhanced their fuel sensor manufacturing course of by an in situ laser-assisted manufacturing strategy, enhancing on their earlier methodology of drop casting, or dropping supplies one after the other onto a substrate utilizing a pipette. They revealed their ends in the Chemical Engineering Journal.
“With drop casting, it’s a must to synthesize every a part of the sensor individually after which combine them, which is logistically difficult, takes a very long time and is dear,” stated corresponding writer Huanyu “Larry” Cheng, James L. Henderson, Jr. Memorial Affiliate Professor of Engineering Science and Mechanics within the Penn State School of Engineering. ”The in situ methodology permits the supplies to be straight synthesized in a single place, and the laser hastens the method.”
Within the course of, a laser inscribes nanomaterials straight on high of a porous graphene foam substrate. The bottom materials permits for the sensor to be stretchy and versatile when utilized on the pores and skin or an object.
In response to Cheng, the strategy opens alternatives to make use of totally different precursors, or nanomaterials, and blend them with totally different ratios and elements. Beforehand, researchers used graphene oxide and molybdenum disulfide to create the sensors. With the brand new methodology, researchers examined 4 extra courses of supplies, together with transition steel dichalcogenide, steel oxides, noble metal-doped steel oxides and composite steel oxides.
“A specific nanomaterial permits us to sense totally different biomarkers or gases, so it is essential for us to get entry to totally different supplies,” Cheng stated. “For instance, one nanomaterial often can solely detect one goal fuel molecule. With a number of decisions obtainable, you may doubtlessly detect extra molecules, enhancing the sensing capabilities.”
Utilizing a number of nanomaterials, researchers created an array of a number of small sensors positioned facet by facet. The capabilities of the array may be in comparison with a human nostril, Cheng stated.
“The nostril developed to detect tens of millions of smells utilizing tens of millions of cells,” Cheng stated. “In the identical method, every of the sensors is ready to detect a unique chemical or particle.”
With the brand new sensor design, researchers eradicated the necessity for a separate warmth supply, additional reducing the complexity of producing the system. The brand new design integrates the gas-sensitive nanomaterials on a single line of porous graphene foam, as in contrast with the outdated design, the place nanomaterials stuffed the gaps between electrodes. The resistance within the single line of porous graphene foam induces Joule warmth for self-heating.
The result’s a classy sensor that has a number of purposes, together with monitoring and alerting the consumer of a fast uptick in gases, similar to on an industrial web site, or an accumulation of gases over time, similar to within the case of air pollution.
Sooner or later, researchers plan to enhance the sensor’s capabilities by programming nanomaterial composites to focus on particular gases or to determine a number of fuel species in advanced mixtures.
Extra info:
Jiang Zhao et al, In situ laser-assisted synthesis and patterning of graphene foam composites as a versatile fuel sensing platform, Chemical Engineering Journal (2022). DOI: 10.1016/j.cej.2022.140956
Supplied by
Pennsylvania State College
Quotation:
In-place manufacturing methodology improves fuel sensor capabilities, manufacturing time (2023, January 20)
retrieved 20 January 2023
from https://phys.org/information/2023-01-in-place-method-gas-sensor-capabilities.html
This doc is topic to copyright. Other than any truthful dealing for the aim of personal research or analysis, no
half could also be reproduced with out the written permission. The content material is supplied for info functions solely.